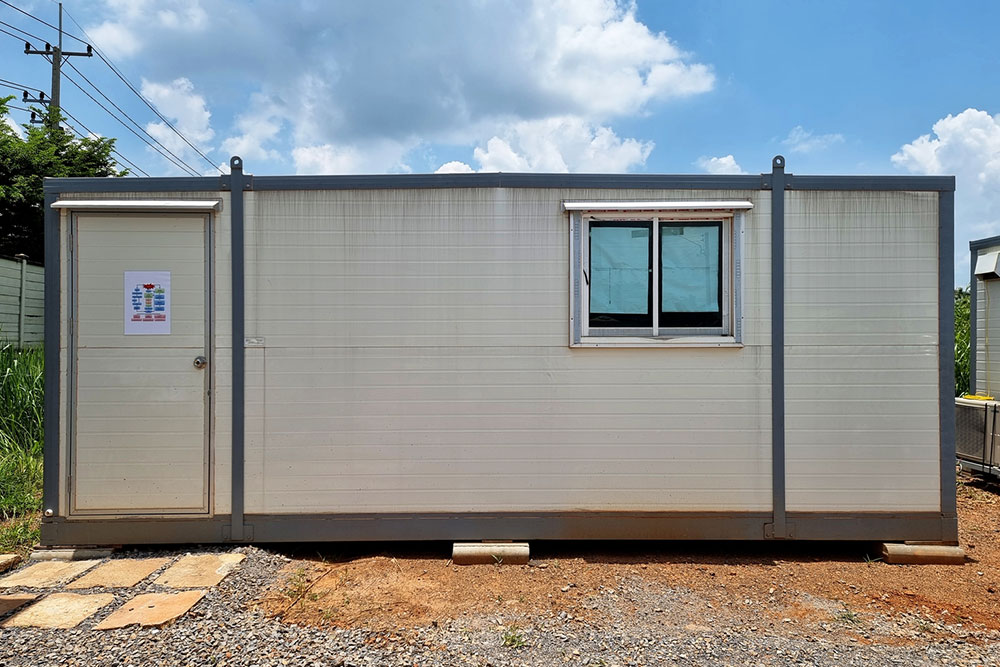
Applications, innovations, and challenges of prefabricated steel structures
Prefabricated steel structures are pre-engineered building components that are manufactured off-site in a factory and assembled on-site later to form complete structures. Also known as prefabs, they offer design flexibility and can be customized to meet specific business needs. These structures are extensively used in industrial buildings, including warehouses, manufacturing and factory plants, and distribution centers. Their cost-effectiveness, rapid construction turnaround, and reusability factor make them a popular choice for various commercial and industrial applications.
Key applications
1. Food industry
Prefabricated steel buildings ensure minimum insect and microorganism intrusion, thanks to their securely sealed structures. They are also easy to clean and disinfect and more likely to adhere to industry standards. Prefab steel buildings also have high load-bearing capacity, which can boost operational efficiency in the food industry. Once the prefab steel structures are well insulated, they can provide efficient temperature and humidity management for refrigerated storage of raw materials or perishable items. It is often used in seafood processing factories since these are enclosed spaces and often have easy-to-clean structures.
2. Industrial facilities
Factories and power plants often use steel structures because they require durable, large, unobstructed spaces that can withstand extreme temperatures, harsh environments, and heavy loads. Since prefabs meet the strength and durability demands of factories, they work well in such areas.
3. Distribution centers
Today’s distribution centers and warehouses require huge spaces and quick loading and unloading turnover. So, prefabricated steel structures are used in these high-load-bearing capacity spaces. These structures can efficiently accommodate heavy equipment and storage racks. Additionally, prefabricated steel allows for versatile layouts and easy expansion, which is crucial for distribution center operations.
4. Apartment complexes
Many apartment complexes require redoing their walls, roofs, and floors over time. Prefabs easily fulfill the demands in such repetitive sections. These structures are known for their durability, low maintenance, and long-term cost-effectiveness. They can be customized to suit various architectural styles, making them a popular choice for apartment complexes.
Innovations
Prefabricated construction has seen innovation in design processes, using modern technologies like Building Information Modeling (BI M) for visualization and planning to precision and Smart Modular Systems for enhanced efficiency and safety. Also, the integration of eco-friendly materials in the prefabrication processes, like recycled steel structures, energy-efficient modules, and smart energy management systems, has made it a more appealing choice. Prefab steels also integrate 3D printing technology to create intricate and customized building elements. With this, there is less scope for human mistakes or oversights. Prefabrication robotics are also a recent innovation that helps boost precision and speed in all areas of construction, from welding and cutting to assembling components.
Challenges
1. Perception
Many traditional industry operators and construction giants are still skeptical about the benefits of prefabs. Most prefab steel buildings have comparatively lower construction costs than traditional buildings. While this is a significant benefit, it also leads to an assumed perception of their quality. Educating stakeholders can help debunk certain myths about prefabs, such as inferior quality or lack of durability, and help them gain more traction.
2. Logistical challenges
Since prefabricated components are assembled mostly on-site, they often require proper transportation and coordinated planning across all stages, especially the execution stage. One must ensure that all the required components are shipped and assembled correctly.
3. Complexity
This may be true in the case of customization since the tailored approach to a particular prefab request means that the construction team may not be well-versed in assembling the new design or components. But one can easily overcome this challenge with innovative design techniques and module systems.